
Här är de verkliga anledningarna till varför väntetiderna för Toyota LandCruiser, Kia Sorento och andra nya 2022-fordon fortfarande är fruktansvärt långa.
Innehåll

Från chips till fartyg till sjuka arbetare, det finns flera anledningar till varför du kanske tycker att det är omöjligt att köpa en Land Cruiser.
Har du testat att köpa en ny bil just nu? För vissa modeller, som Toyota Landcruiser 300 och RAV4 eller Volkswagen Amarok, måste du vänta många månader, kanske upp till sex månader eller till och med längre, för att få efterfrågade varianter.
Tror du att du kan undvika detta genom att köpa något lite begagnat istället? På vissa sätt är detta det värsta du kan göra. Marknaden för begagnade bilar har uppmärksammat bristen på nya bilar, med både privata säljare och begagnade bilhandlare som ägnar sig åt gammaldags prismätning, särskilt på stadsjeepar och stadsjeepar. Har du funderat på att köpa en Suzuki Jimny från begagnade bilmarknaden? Gör inte detta om du inte är villig att betala en femsiffrig premie över detaljhandeln.
Men varför finns det fortfarande så få bilar tillgängliga två år in i pandemin? Har pandemin fortfarande skulden? Svaret är enkelt: "eftersom datorchips"? Å nej. Situationen är lite mer komplicerad, men för att förstå varför måste vi först förstå hur fordonsförsörjningskedjor fungerar.
Kedja av svaga länkar
Allt hänger ihop. Allt. Det finns heller ingen slack i den globala leveranskedjan. När leverantören ger upp sin del av denna metaforiska kedja kommer konsumenten också att känna det på sin sida.
Detta beror till stor del på en branschpraxis som kallas just-in-time manufacturing, även känd som lean manufacturing. Den utvecklades först av Toyota under första hälften av förra seklet och användes av praktiskt taget alla biltillverkare sedan dess, och gjorde det möjligt för biltillverkare att eliminera behovet av att upprätthålla stora lager av delar, sammansättningar och råmaterial och istället säkerställa att mängden delar som beställdes från leverantörer motsvarade deras kvantitet. Det finns inga fler delar, och absolut inte mindre, av de delar som faktiskt behövs för att tillverka bilar. Det eliminerade slöseri, ledde till en mycket effektivare försörjningskedja, ökad anläggningsproduktivitet, och när allt fungerar som det ska är det praktiskt taget det bästa sättet att sätta ihop bilar till ett överkomligt pris.
Detta är dock inte ett system som är särskilt motståndskraftigt mot misslyckanden.
Så för att minimera risken för att en hel monteringslinje stängs av eftersom en leverantör inte kunde få ihop det, kommer biltillverkare att använda det som kallas "multisourcing". Från däck till enskilda muttrar och bultar, en komponent har sällan bara en källa, och ofta kommer det att finnas flera om delen används flitigt på en produktionslinje över flera modeller. Slutkonsumenten kommer inte att veta om plasten till deras dörrar levererades av leverantör A eller leverantör B - kvalitetskontroll säkerställer att de alla ser ut och känns likadana - men det betyder att om leverantör A har problem på sin egen monteringslinje, leverantör B kan ingripa. och se till att tillräckligt med dörrplast kommer in i bilfabriken för att hålla linjen öppen.
Leverantörer A och B är kända som "tier one-leverantörer" och levererar färdiga delar direkt till biltillverkaren. Stora problem kan dock uppstå när alla dessa förstklassiga leverantörer använder samma leverantör för deras råvaror, som kommer att kallas en andra leverantör.
Och detta är i princip läget när det kommer till nästan allt som är elektroniskt i en bil. Om en bildelar kräver en mikroprocessor av någon beskrivning, är källorna till kiselchipsen som utgör dessa mikroprocessorer löjligt centraliserade. Faktum är att bara ett land – Taiwan – står för lejonparten av kiselchips (eller halvledare) med hela 63 procent av den globala marknaden för halvledarbasmaterial, där den stora majoriteten kommer från ett företag: TMSC. När det kommer till färdiga chips och elektronik står USA, Sydkorea och Japan för större delen av marknaden, med endast en handfull företag i dessa regioner som levererar mikroprocessorer till praktiskt taget hela världen.
Naturligtvis, när andra klassens mikroprocessorleverantörer saktade ner produktionen på grund av pandemin, var deras kunder – alla dessa första leverantörer – tvungna att göra detsamma. På grund av bristen på mångfald i den här änden av försörjningskedjan räckte det inte med flera inköpsmetoder för att hålla monteringslinjerna för världens biltillverkare igång.
Situationen har förvärrats av biltillverkares misslyckande med att förutse fortsatt hög efterfrågan på fordon under pandemin, men även när vissa biltillverkare skrotar fordon för att minska antalet chips som behövs (Suzuki Jimny, Tesla Model 3 och Volkswagen Golf R två nyligen exempel) det finns andra faktorer...
Fartygssituation
På tal om ömtåliga ekosystem, världen av global sjöfart är lika upptagen som biltillverkning.
Vinstmarginalerna på sjöfrakt är inte bara förvånansvärt snäva, utan fartyg som transporterar containerlast är också otroligt dyra att driva. Med pandemin som stör leveranskedjorna men också orsakar oväntad efterfrågan på konsumtionsvaror, har flödet av fartyg och containrar störts allvarligt, vilket inte bara har lett till omfattande förseningar utan också ökade fraktkostnader.
Huvuddelen av konsumtionsvarorna kommer från Kina och Sydostasien, och när en produkt skickas från den delen av världen till en annan, fylls containrarna som bär den lasten vanligtvis på nytt med produkter från destinationslandet och omlastas till ett annat. Fartyget återvänder så småningom till Sydostasien för att slutföra cykeln igen.
Men med stark efterfrågan på kinesiskt tillverkade varor men begränsad efterfrågan på varor som gick åt andra hållet, hamnade en hel massa containrar i hamnar i Amerika och Europa, och fartygen gick sedan tillbaka till Asien med lite eller ingen last ombord . Detta störde distributionen av containrar runt om i världen, vilket ledde till en brist på containrar i Kina, vilket sedan ledde till massiva förseningar i sjötransporter av allt som producerats i regionen – både konsumtionsvaror och råvaror, av vilka en del behövdes i produktionen linjer bilar.
Och, naturligtvis, eftersom moderna produktionslinjer bara går när delar levereras precis i tid, resulterar det i att många monteringsfabriker står stilla och väntar på att komponenter och material ska komma – komponenter och material som inte nödvändigtvis är bland de första som kommer. med mikrochips inuti.
Du kan inte bygga en bil hemma
Om du är en tjänsteman är det förmodligen en välsignelse att arbeta hemifrån. Om ditt jobb kräver att du arbetar med verktyg i en bilmonteringsfabrik, ja... det är inte så att du kan montera en Kluger på ditt köksbord.
Anmärkningsvärt, trots detta, har många industrier kunnat fortsätta fungera under hela pandemin, men medan fabriksarbetare i många delar av världen fortfarande kan använda verktyg, har det fortfarande förekommit en viss grad av störningar i deras arbetsflöde.
Först var företagen tvungna att göra arbetsplatserna tillräckligt säkra för sina arbetare. Detta innebär att konfigurera om arbetsutrymmen för att rymma social distans, installera skärmar, beställa personlig skyddsutrustning, omorganisera raster och omklädningsrum – listan fortsätter. Denna process tar tid. Att arbeta skift med färre personal har också varit en annan strategi för att hålla arbetarna säkra, men det har också en inverkan på produktiviteten.
Och vad händer sedan när det är ett utbrott. Toyotas senaste produktionsavbrott berodde till stor del på att arbetare blev sjuka, med bara fyra sjukdomar tillräckligt för att stänga företagets Tsutsumi-fabrik i Japan. Även om fabriker inte stänger när någon blir sjuk, så påverkar arbetarnas frånvaro på grund av karantän fortfarande fabrikens produktivitet på grund av hur vitt covid-19-viruset har spridits.
Så... när tar det här slut?
Det finns ingen central orsak till att bilar nu är svåra att få tag på, utan snarare många sammanhängande orsaker. Det är lätt att skylla på COVID-19, men pandemin var bara den utlösande faktorn som fick korthuset som är den globala bilförsörjningskedjan att kollapsa.
Men allt kommer så småningom att återhämta sig. Det finns mycket tröghet i saker som chiptillverkning och global frakt, men återhämtningsutsikterna är goda. Det återstår dock att se hur branschen kommer att isolera sig från en upprepning av detta scenario.
När det gäller när återhämtningen kommer att ske är det osannolikt att det händer i år. Kort sagt: om du har råd att vänta lite längre med att köpa din nästa bil kan du spara pengar och minska din väntetid. Oavsett vad, ge inte efter för dessa flagranta spekulanter på andrahandsmarknaden.

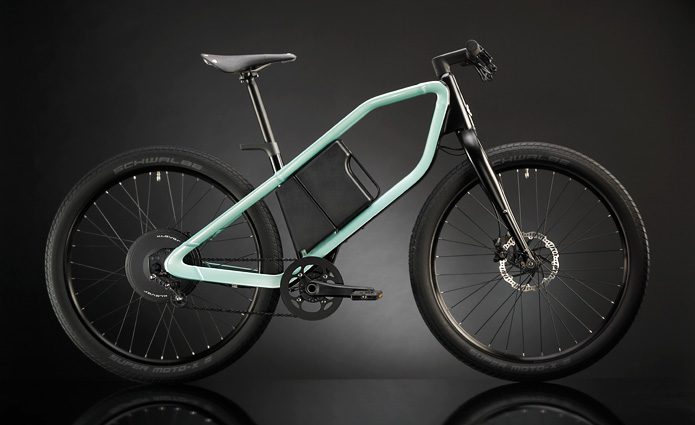